On-Demand EMC Services for Modern Electronic Companies
Identify & Solve EMC/EMI issues at any stage of your hardware development project and launch EMC-compliant products faster to market.
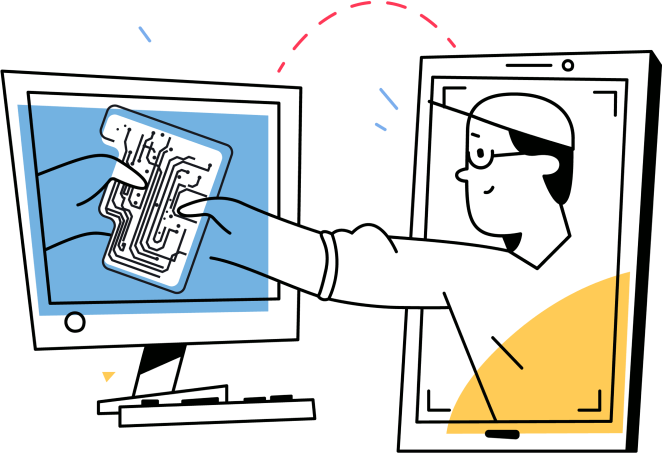
Real feedback from our customers who use DENPAFLUX
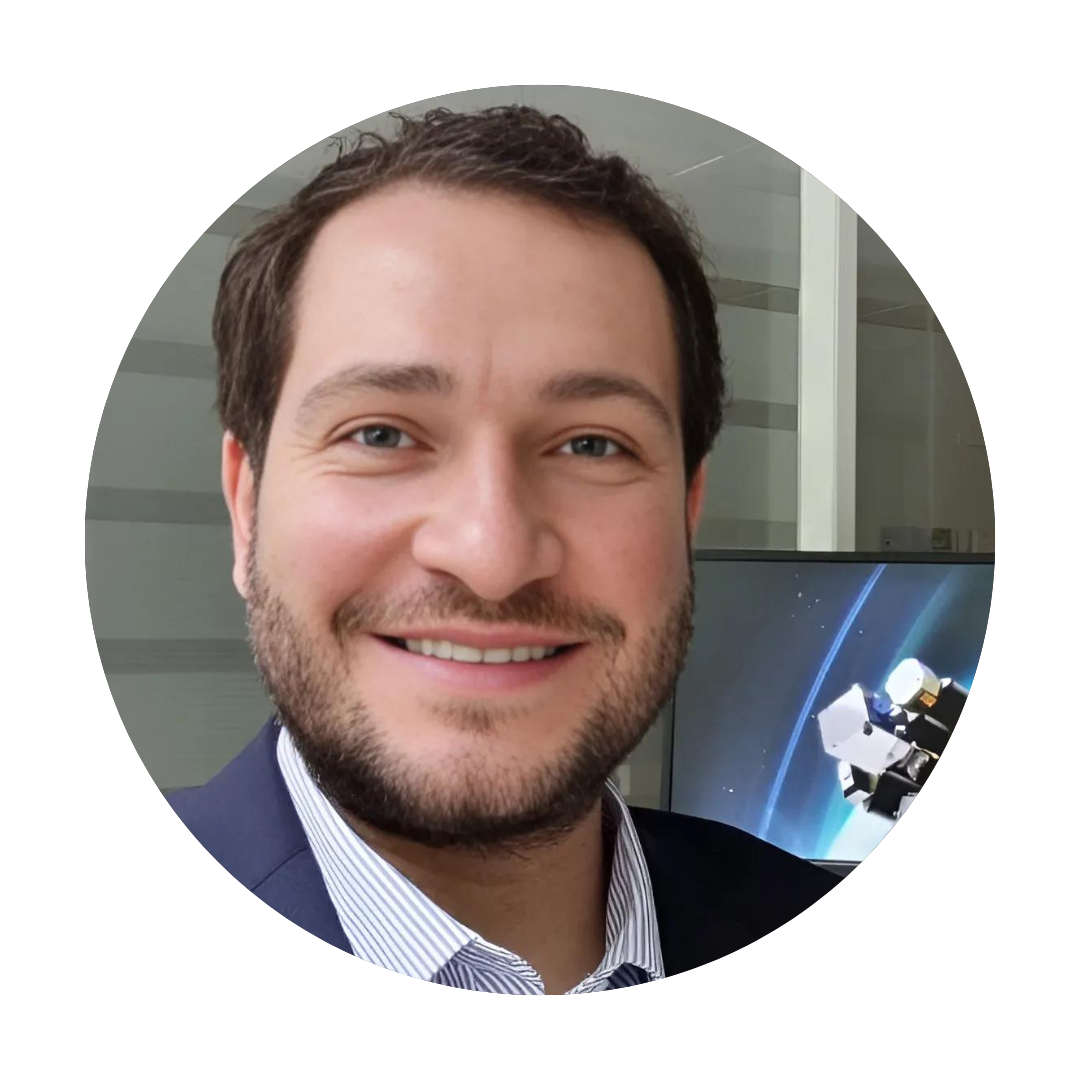
Thanks to DENPAFLUX, we were able to identify and fix potential EMC issues early in the design process, allowing our engineers to fast-track iteration and fewer re-spins on designs which saved us a lot of time and money down the road.
One of the biggest benefits of working with DENPAFLUX was their easy-to-understand and concrete mentions in the report. EMC recommendation reports were classified by severity, making it easy for us to understand the findings and take action on them. We couldn't be happier with the results.
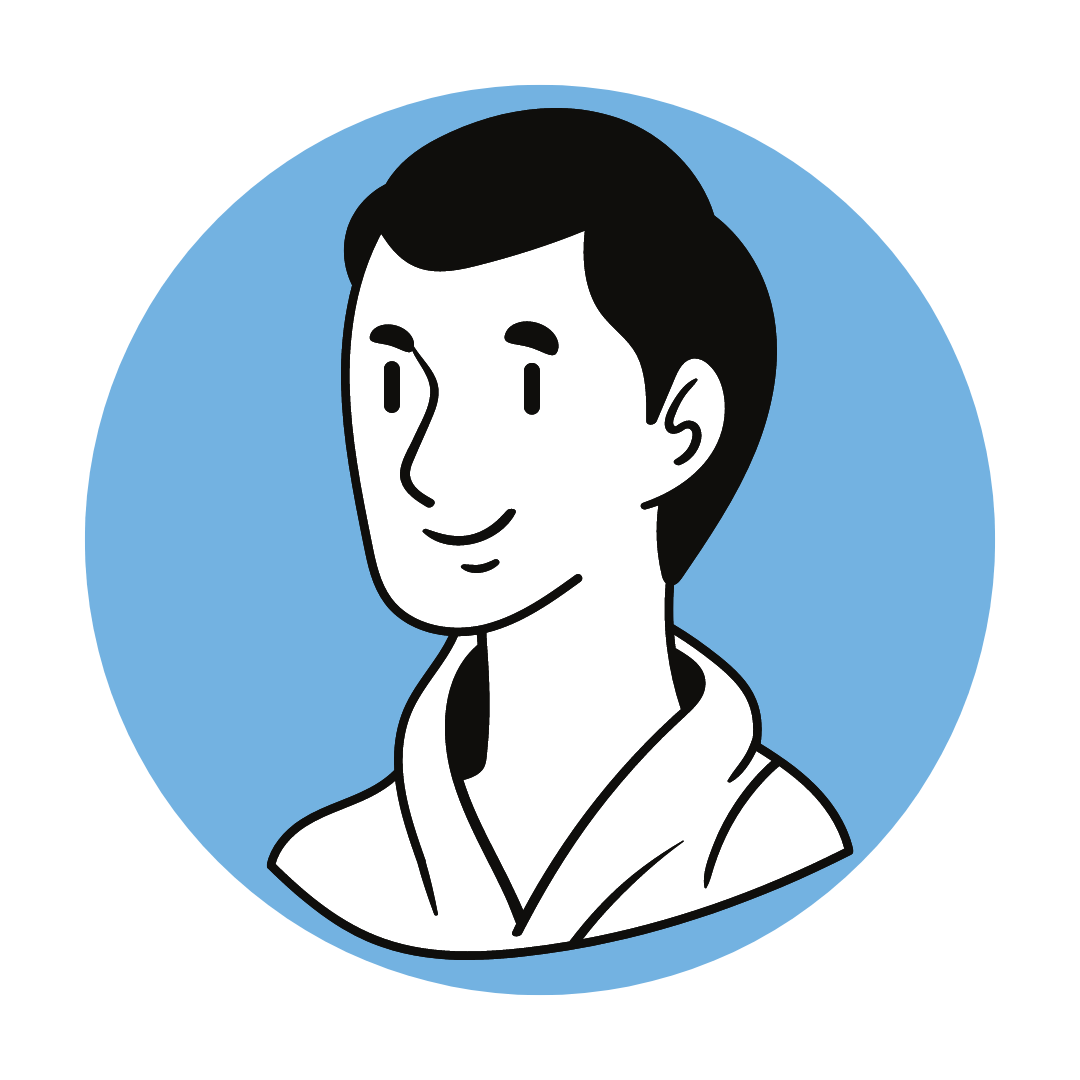
DENPAFLUX prompted our team of design engineers to thoroughly revisit and analyse the specific design elements in question, resulting in enhanced rationale for our design decisions They empowered us to achieve optimal solutions and strengthen our design process!
To ensure that we don’t lose months
to a redesign we use DENPAFLUX to check for possible EMC problems. Having another AI-powered pair of eyes meticulously checking every circuit will always be beneficial. The knowledge and best practice techniques learned from the detailed reports also help us in avoiding certain error sources from the get-go.
Experience DENPAFLUX Way to Solve your EMC Challenges
See how DENPAFLUX helps electronics design teams to eradicate EMC issues faster & easier by providing iterative consultation as of the early product development cycle with our AI-infused EMC service.
The Hidden Cost of Solving EMC at Later Stage of Product Development Cycle
70
%
4
weeks
50
%
Customer Story: How DENPAFLUX's EMC Services Cut eeProperty's Product Development Time by 50% ?
Discover how DENPAFLUX helped eeProperty solve critical EMC issues in their smart building technology, improving test performance
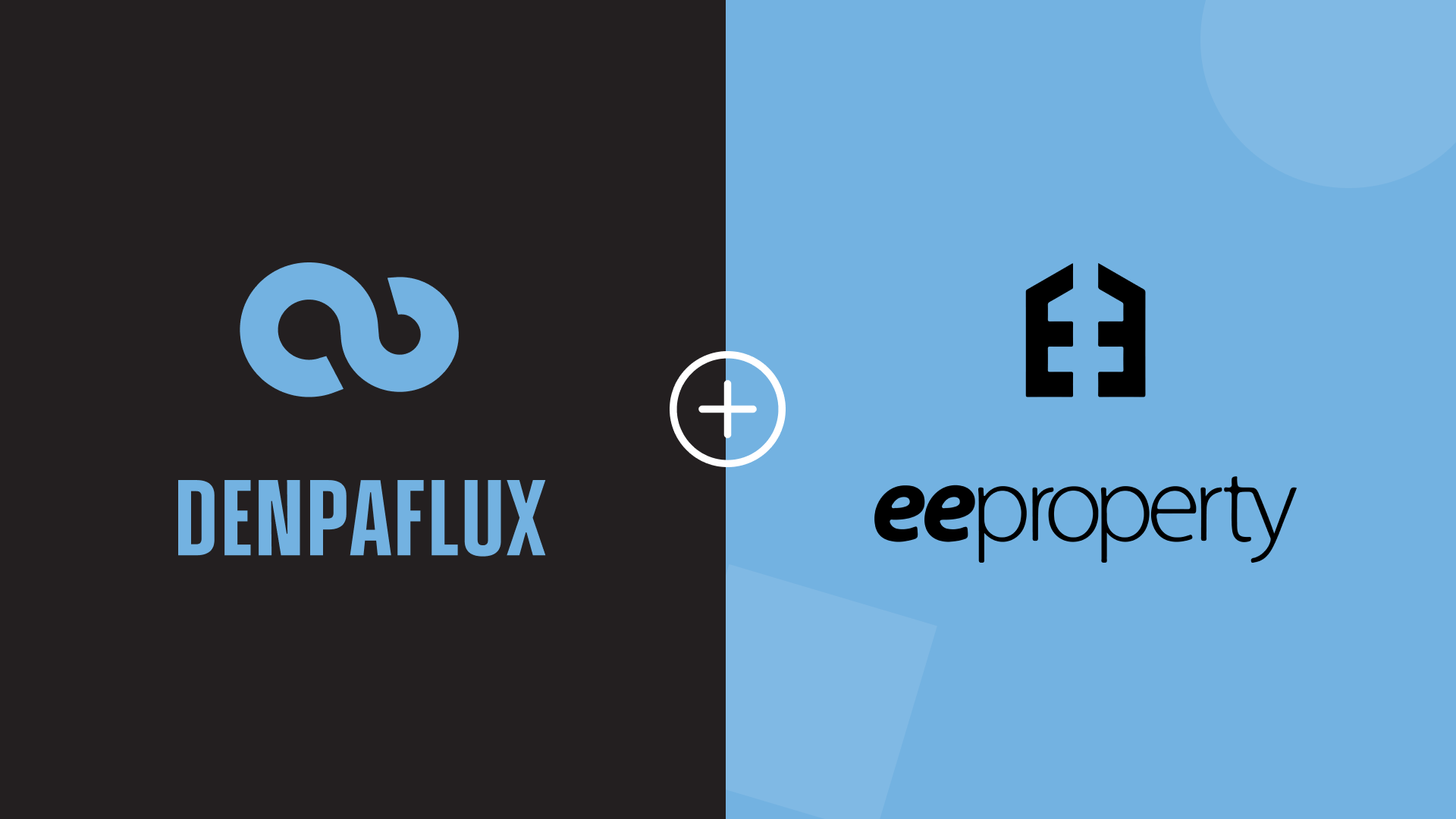
EMC Services Aligned with Your Hardware Development Project
Concept & Planning
- Standards identification and planning
- Architecture review and guidance
- Component selection support
- Early risk assessment
Design Phase
- Architecture and grounding review
- Filter design and simulation
- Protection design verification
- Wiring and mechanics assessment
EMC Pre-Compliance
- Pre-compliance testing setup
- EMC issue identification
- Mitigation strategy planning
- Design iteration support
EMC Certification Support
- Test plan development
- Lab coordination support
- EMC testing assistance
- Results analysis and reporting
Worried about IP rights ?
Our digital NDA takes less than 1 minutes to complete.
Self-sign your NDA and share your electronic design projects confidently and get personalised EMC guidance from our experts.
Industry's first interactive EMC visualisation platform!
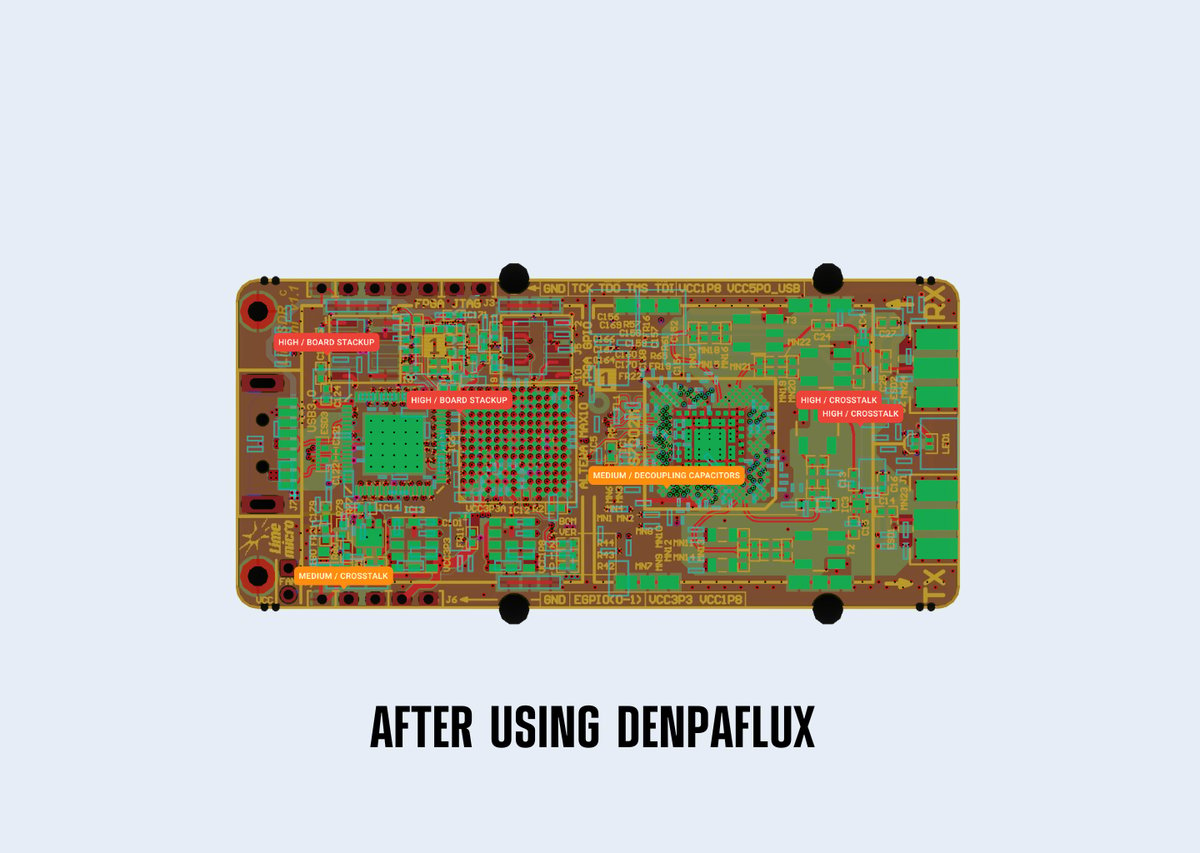
Advanced EMC Insights
Interactive EMC Issue Viewer
Identify and address potential EMC issues at the earliest stages of design. Our advanced platform analyzes your designs proactively, saving countless hours of manual troubleshooting while ensuring both compliance and optimal functionality. Stop reactive EMC problem-solving and start designing with confidence
Detailed EMC Review
EMC Review Directly on Your Electronics Design
No more guesswork in EMC troubleshooting. Our interactive viewer shows exactly where and why EMC issues occur in your PCB design. Engineers report 60% faster issue resolution when they can visualize EMC problems directly on their designs
Smart Prioritization
Intelligent EMC Issue Prioritization
Focus on what matters most. Stop wasting time on minor issues while critical EMC problems remain unresolved. Get a structured approach to EMC problem-solving.
EMC Success Story (PDF)
How DENPAFLUX Eliminated Critical EMC Issues and Cut 73 Days From Development Time ?
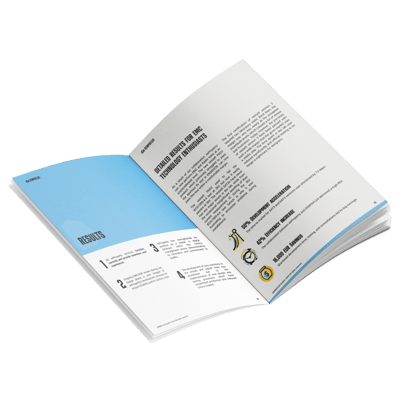
SIMPLE PLAN, FLEXIBLE PRICING
We believe in individual solutions. Every product, every project, and every schematic is unique. Our approach is tailored to your specific needs, industry requirements, and business goals.
- 1 Project
- 2 Iterations
- 2 EMC Expert Calls
- 2 Months Plan
- 1 Project
- Unlimited Iterations
- 5 EMC Expert Calls
- 12 Months Plan
- Live EMC Trainings*
- 3 Projects
- Unlimited Iterations
- 12 EMC Expert Calls
- 12 Months Plan
- Live EMC trainings*
- We create amazing digital products.
- We create amazing digital products.
- We create amazing digital products.
- We create amazing digital products.
- We create amazing digital products.
Frequently Asked Questions About DENPAFLUX
How does the process of working with DENPAFLUX typically works?
DENPAFLUX is simple and efficient. We start with a no-obligation call to understand your EMC challenges. Based on this, we create a customized plan aligned with your chosen package that includes design reviews, consulting, EMC testing, and access to our AI-powered platform. Upon completion of the initial purchase order or payment, you'll have immediate access to our platform and services, allowing you to promptly address your EMC requirements.
What kind of design file you need to work with DENPAFLUX?
DENPAFLUX accepts all major CAD software files, including Altium, KiCad, and Eagle. We also work with schematic diagrams, system-level designs like cabling, and even PDFs. We easily integrate with your current workflow, enhancing your existing processes without disruption.
How does DENPAFLUX ensure the confidentiality of our designs when we upload them for analysis?
We take your intellectual property very seriously. All design files are secured during transmission and storage. We offer a self-sign NDA before you share any designs, and our platform adheres to strict data protection protocols
We're a small team with limited EMC expertise. Can DENPAFLUX still help us?
Absolutely! In fact, smaller teams often benefit the most from our services. We not only provide tools and analysis but also education and training. Our experts can guide your team through EMC best practices, helping you build in-house expertise while solving immediate challenges.
Do You Have More Questions for us ?
Talk to our expert: Book a no-obligation call
Meet Our EMC Experts Ready to Solve Your Design Challenges
With decades of combined experience across industries, our EMC specialists provide hands-on expertise from concept to certification. We've helped hundreds of companies overcome complex EMC challenges and build better products
European Market
UK Market
USA & Canada Market
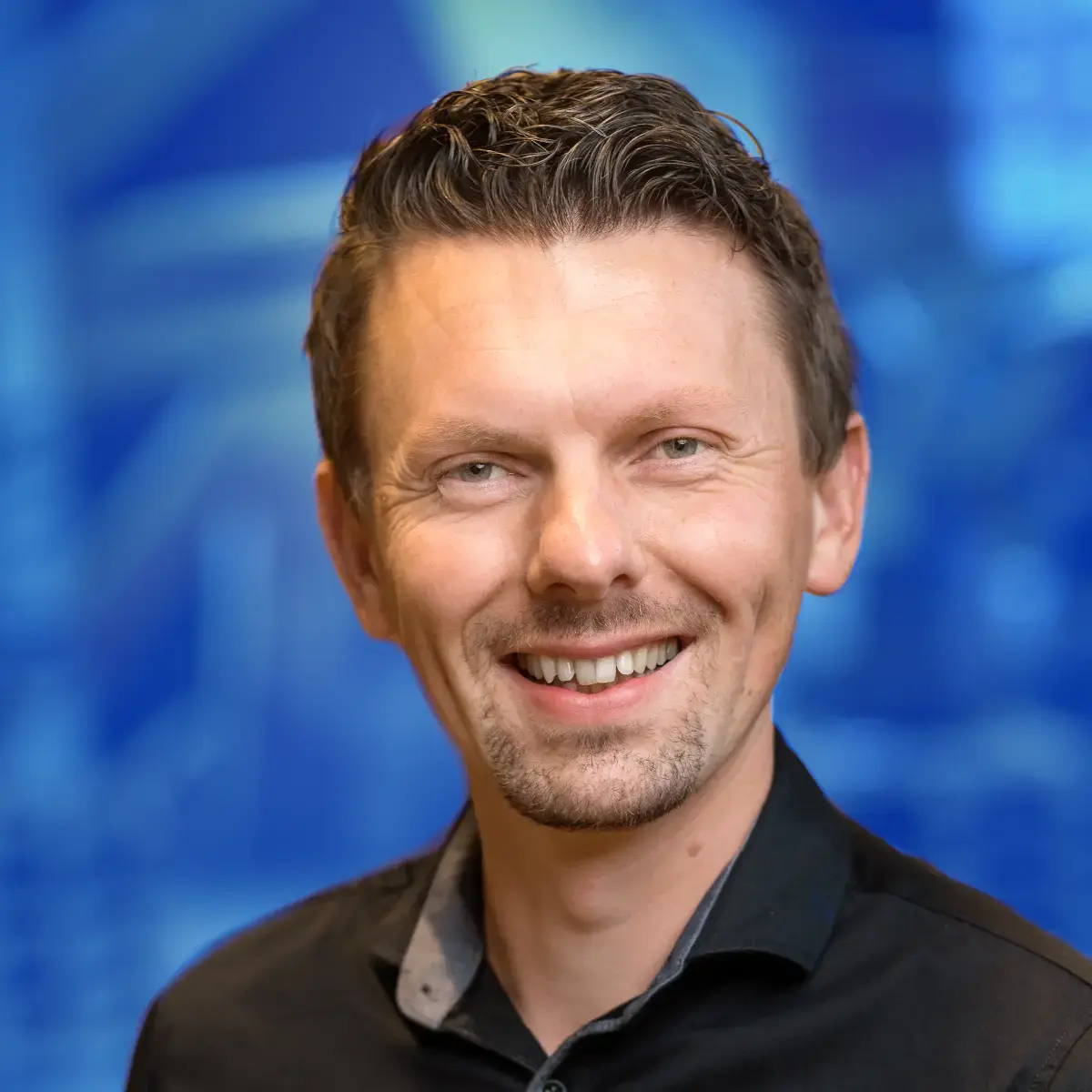
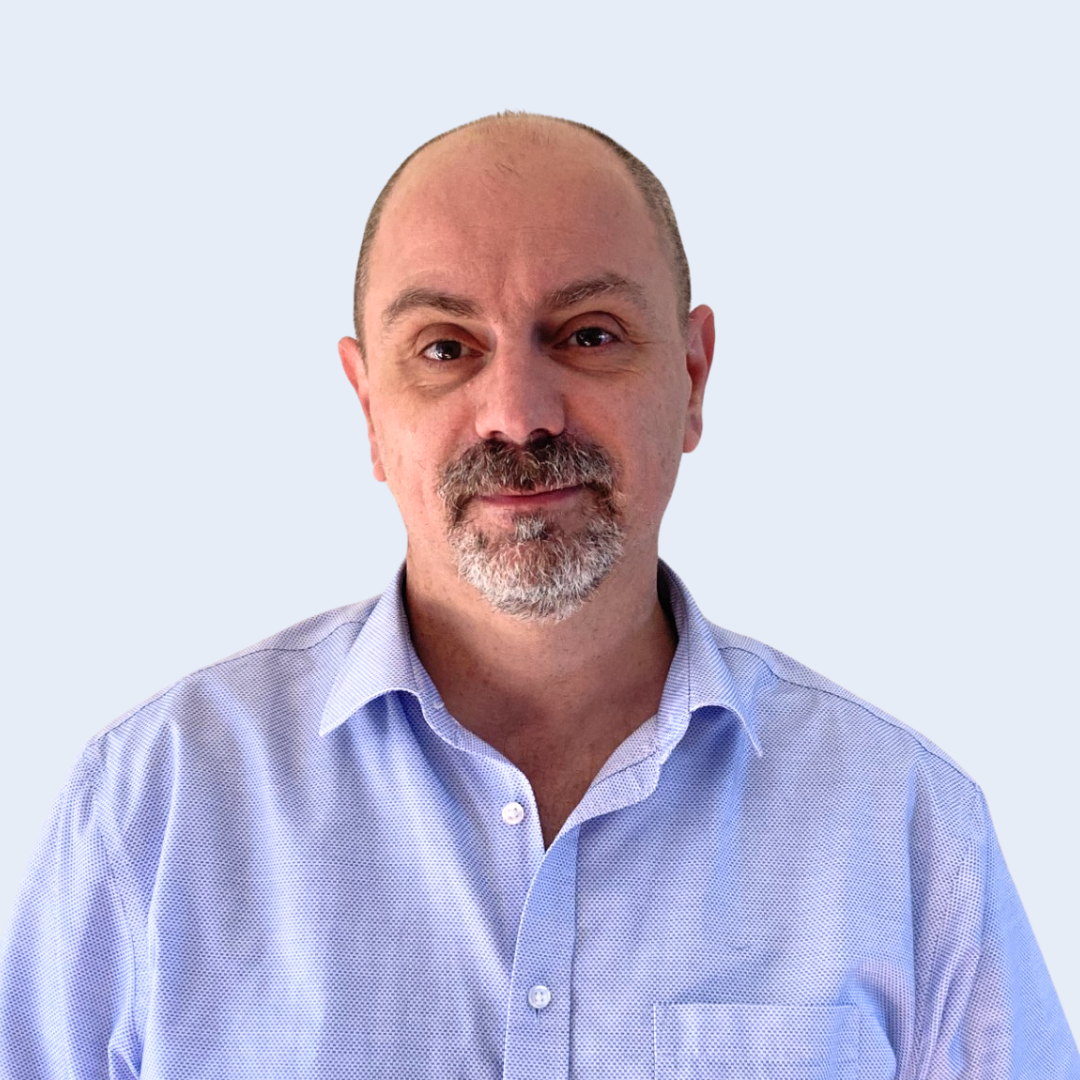
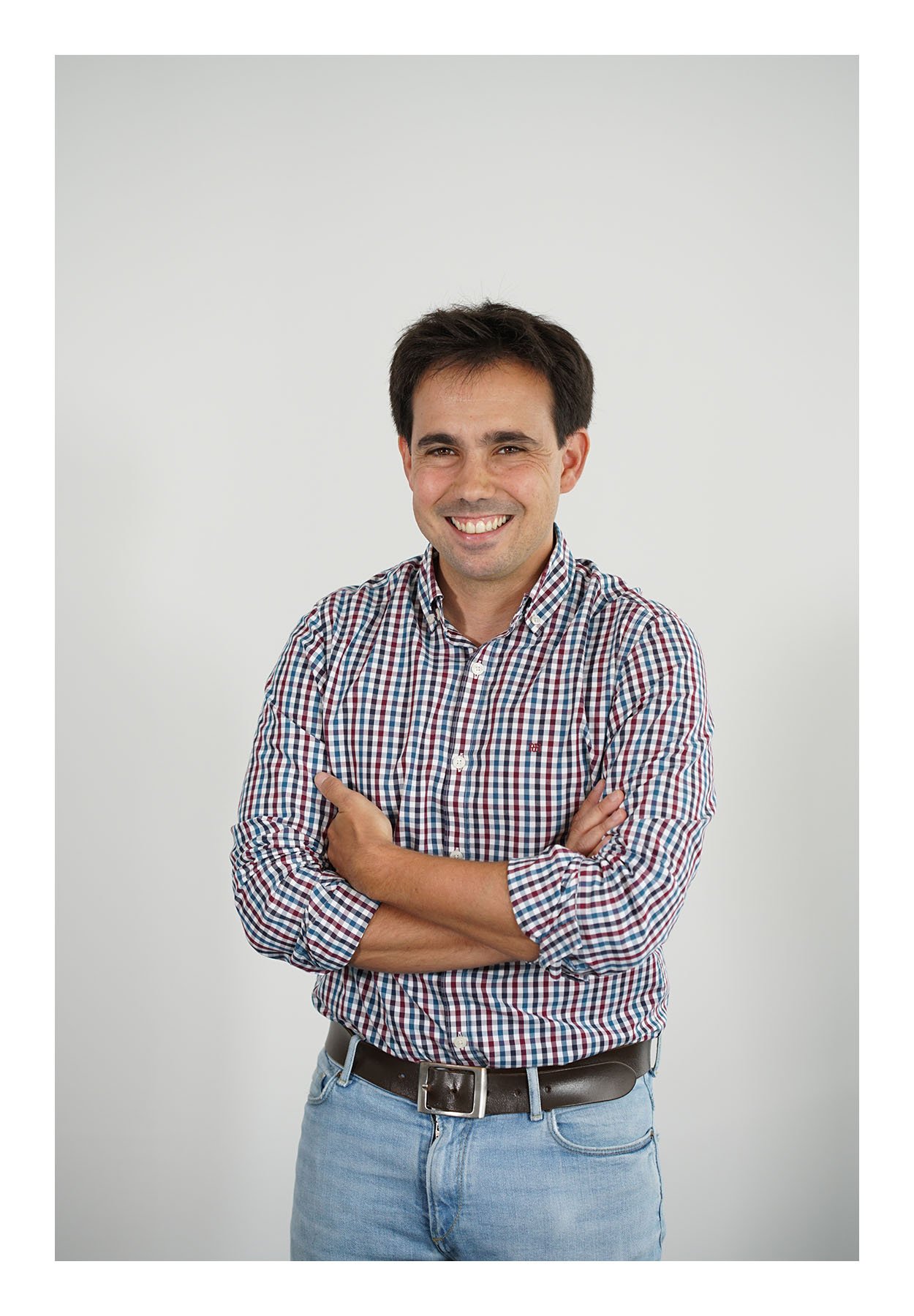
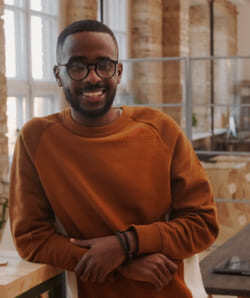